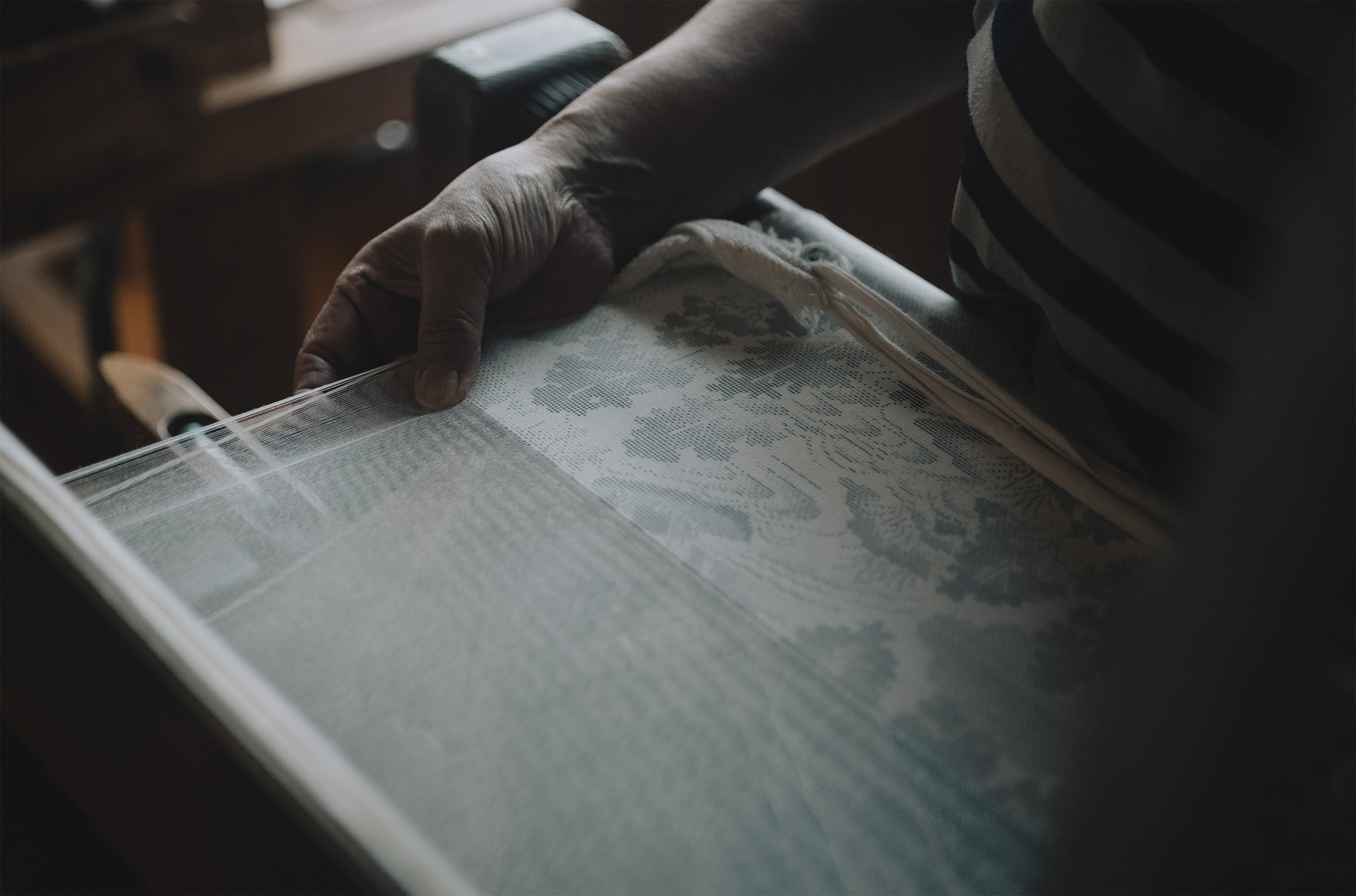
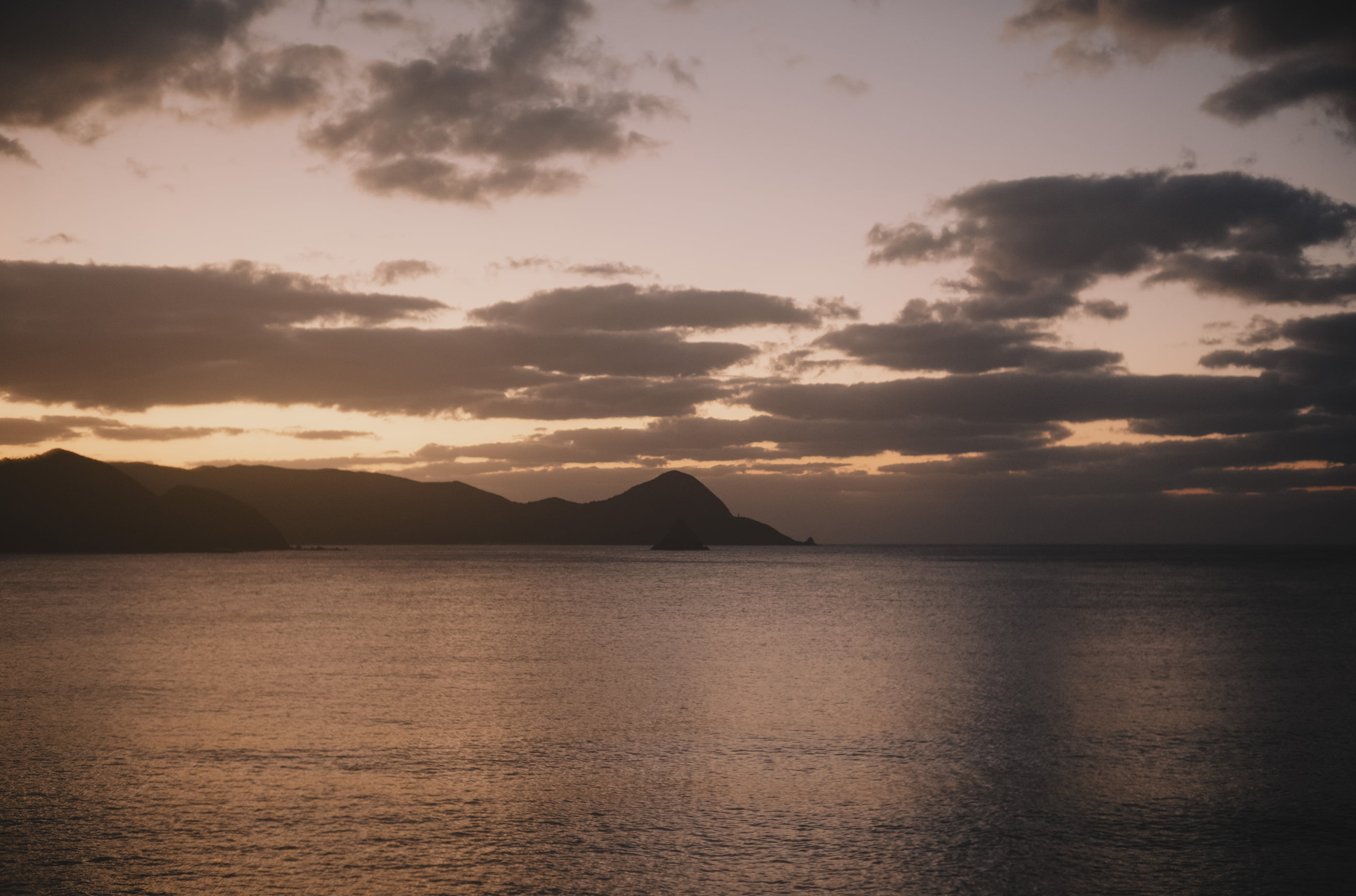
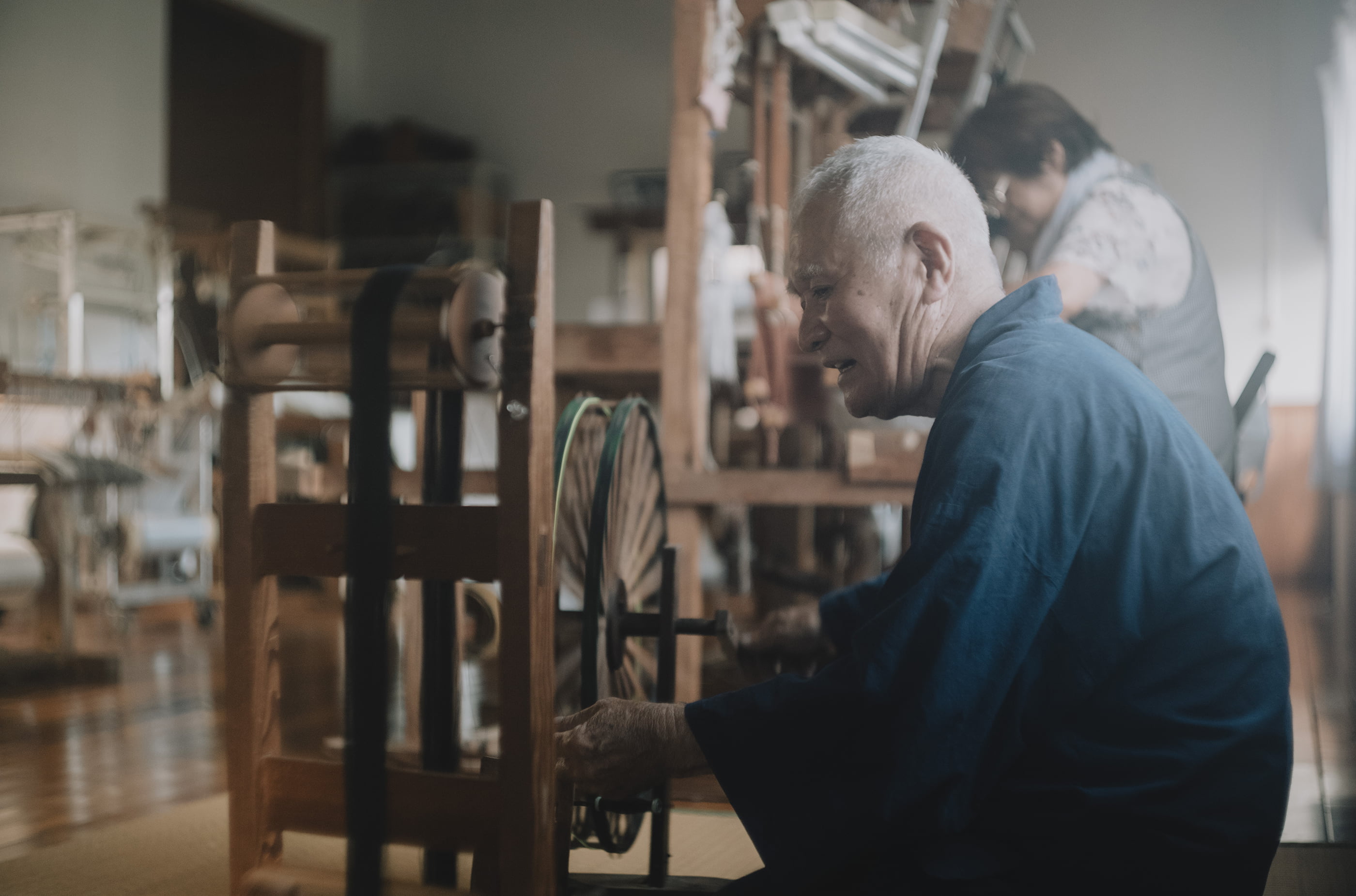
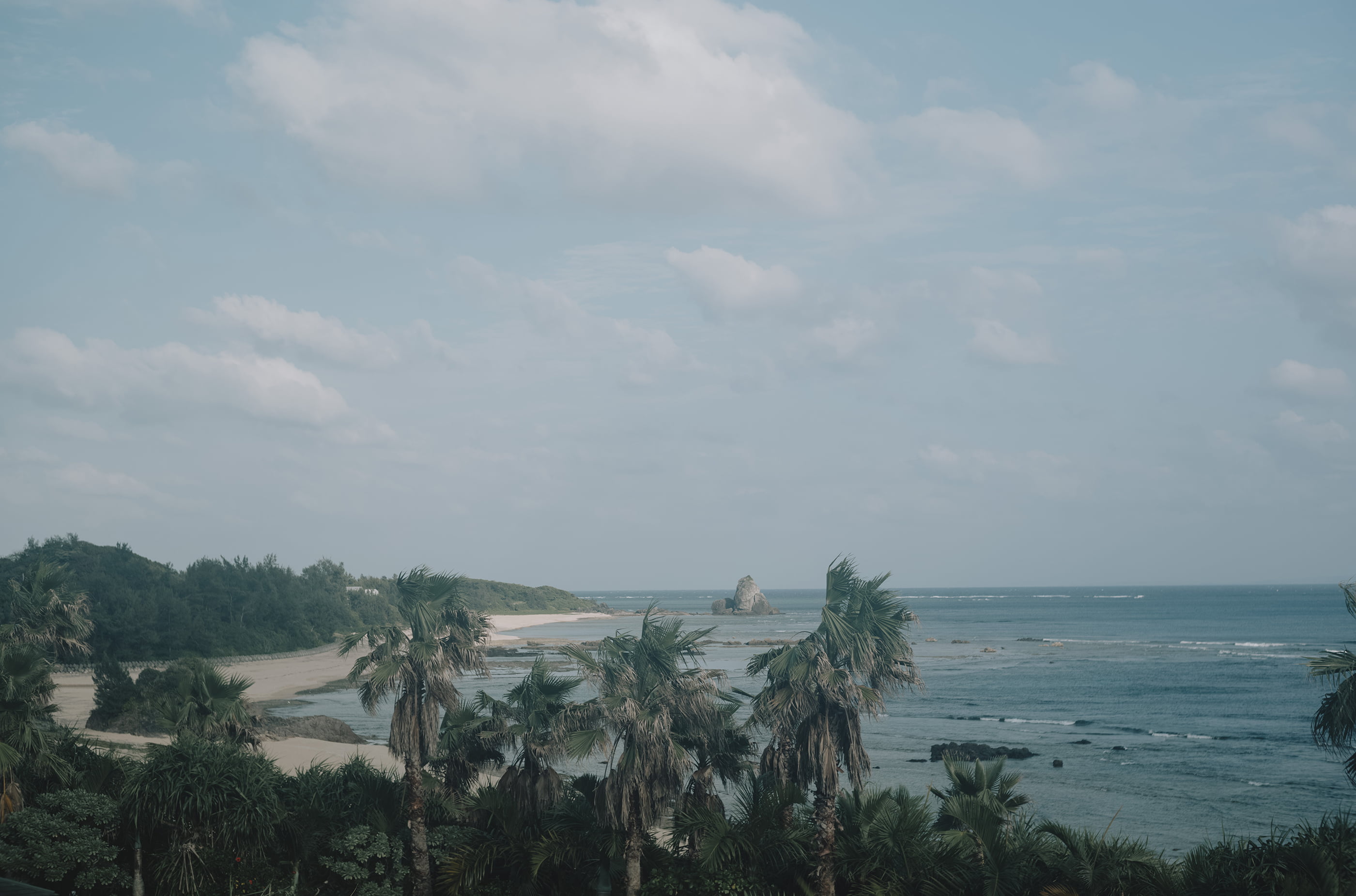
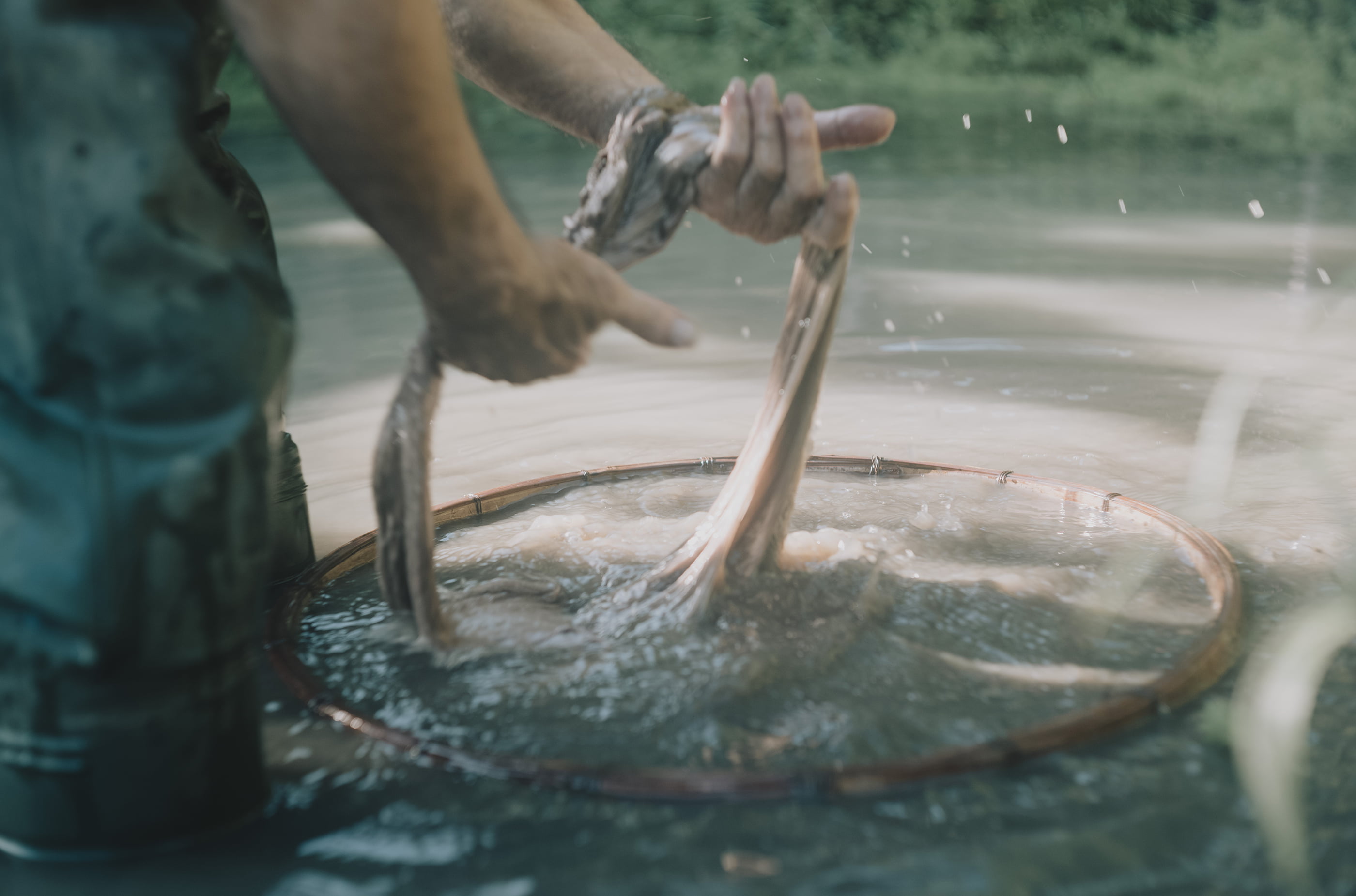
About
About OSHIMA TSUMUGI MUSUEM
We believe that Oshima Tsumugi is a work of art.
We plan and produce this wonderful Oshima Tsumugi, and carefully store both historical masterpieces and new works until we hand them over to customers who understand their value.
As such, we decided that calling this place a “museum” was the only choice we had.
Some of you may think that it is an overstatement.
However, the word “art museum” is the embodiment of our long-held dreams.
In other words, it shows the determination we have to create wonderful Oshima Tsumugi that resembles works of art.
Katsuyo Higo, Representative Director
About Oshima Tsumugi
Oshima Tsumugi refers to silk fabric produced mainly on Amami-Oshima Island, and to kimonos made from the fabric. The process of yarn-dyeing, shaping, and weaving of twisted silk yarns is all done by hand by craftsmen. The silk fabric is characterized by its unique plant-derived colors and dyed patterns. It is lightweight and can be worn in any season or setting, so it has long been popular as both ceremonial dress and everyday wear.
The process involves numerous steps that include designing, gluing, kasuri fastening, Yeddo hawthorn dyeing, and mud dyeing. Depending on how you count it, there are said to be more than 100 steps involved in this dizzyingly detailed work. Dozens of craftsmen are involved in the processes required to create each piece of cloth.
- ● Shimebata
-
Oshima Tsumugi has two weaving processes, the first of which is done with a loom called a “shimebata”. In this step, colored and uncolored yarns are woven according to the design, and cotton threads for the weft and warp of the fabrics are woven in to create what is called “kasuri mushiro”.
- ● Mud Dyeing
-
After dyeing the fabric brown with fermented extract from the Yeddo hawthorn bush, the fabric is soaked in a mud field, rinsed, and dried, a process that is repeated over and over again. The natural chemical reaction that occurs between the Yeddo hawthorn and the iron content of the mud field dyes the silk threads black, producing a natural black color.
- ● Dyeing Materials
-
In addition to the Yeddo hawthorn bush that grows naturally on Amami-Oshima Island, sago palm leaves are essential for the muddy fields as raw materials. Adding the sago palm leaves replenishes the iron content of the mud field, creating a suitable environment for the dyeing process. Sago palm is also cherished as a traditional pattern for silk pongee.
- ● Kasuri
-
After the kasuri mushiro have been woven on the shimebata and dyed with mud, they are unraveled so that only the warp and weft kasuri yarns remain. These are then woven together according to the design to create the intricate patterns and unique texture that Oshima Tsumugi is known for.
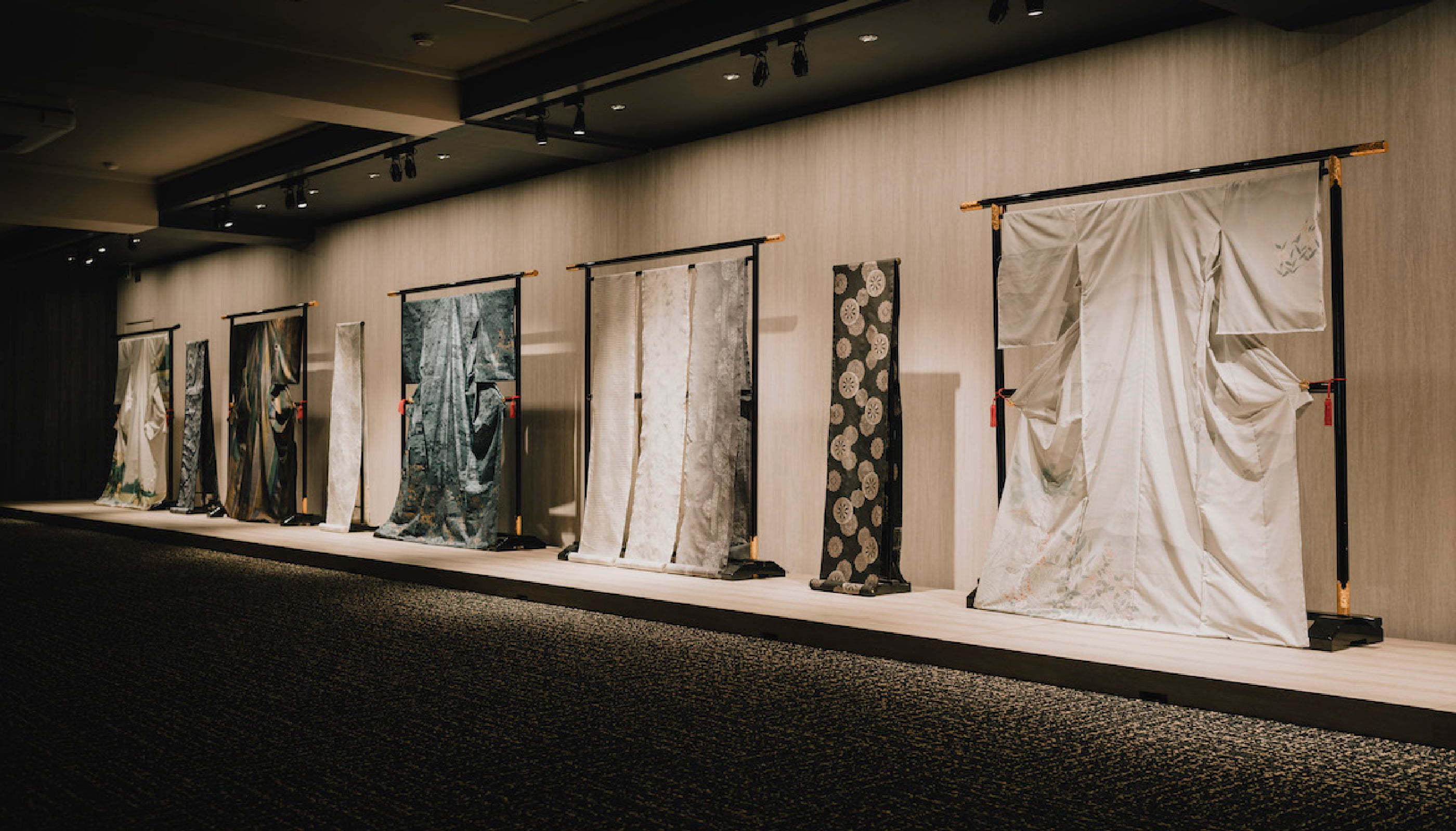
-
About the Oshima Tsumugi Museum
Oshima Tsumugi Museum Co., Ltd. is a producer and seller of Oshima Tsumugi that, in addition to manufacturing kimono, has also developed a variety of businesses in order to create a community that can preserve and pass on the natural climate, human activities, and kimono culture at the heart of Oshima Tsumugi to future generations.
- ・The weaving business that ranges from production to sales
- ・An art museum that preserves and passes on Oshima Tsumugi as an art form
- ・Accommodation facilities that allow visitors to experience the culture of the island
- ・A museum to show the history and manufacturing process of Oshima Tsumugi
- ・The Kusaki Mud Dyeing Laboratory which is both a factory and dyeing facility
- ・Other events
-
What is to come
It is said that “many weavers are good at island songs”, and many weavers sing while weaving. Oshima Tsumugi incorporates the culture of the land of Amami, including the lifestyle of the island and the character of the people.
It is precisely because we live in such an era that we will continue our activities with a strong will to preserve authentic techniques.
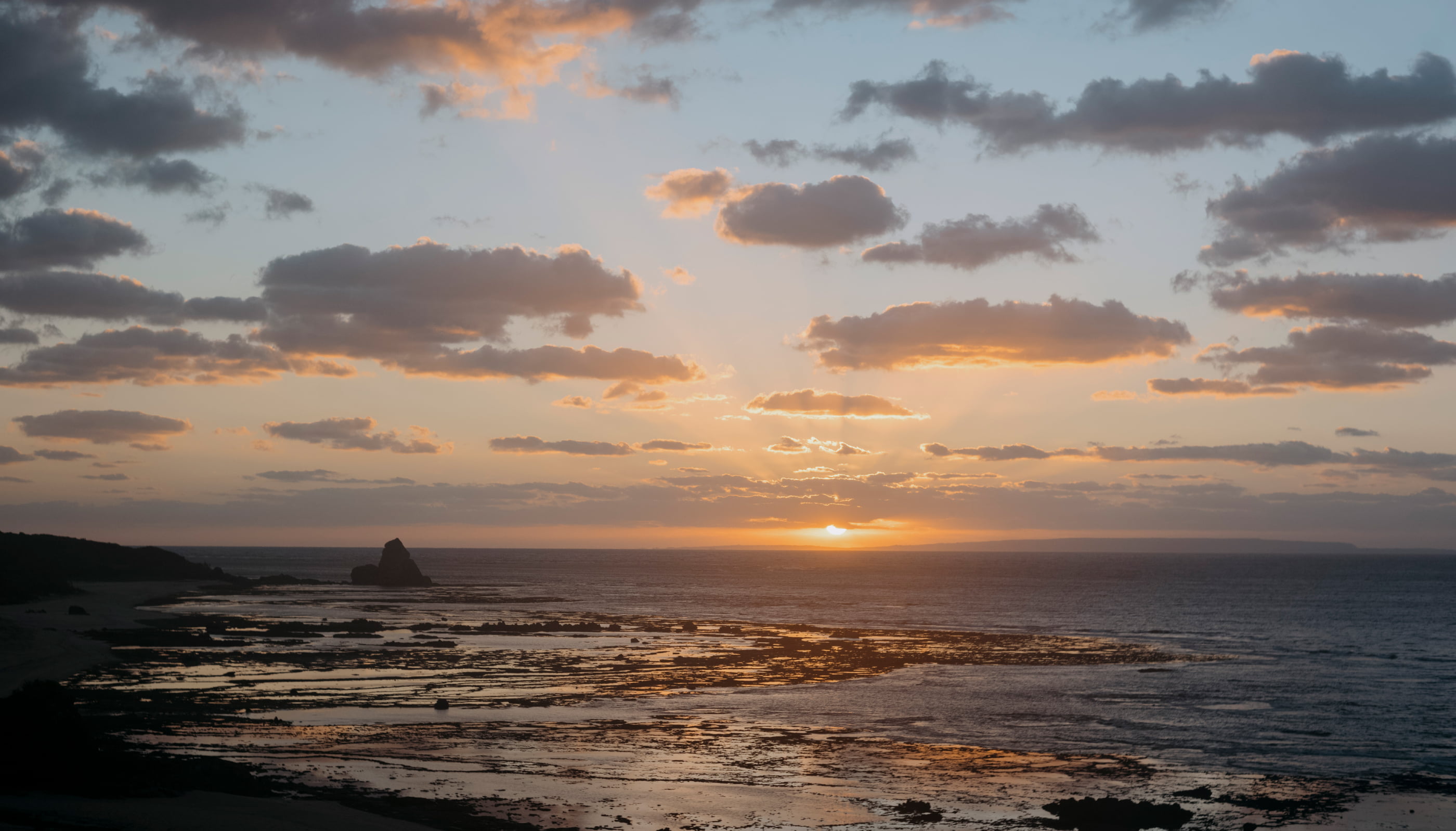
Contact
For inquiries about studio tours, exhibitions, museums, interviews, employment, etc.,
please feel free to contact us by phone or e-mail.
- Tel: 0997-63-0065
Hours: Weekdays 10:00-17:00
- Mail: info@oshima-tsumugi.com
Company
OSHIMA TSUMUGI MUSEUM CO., LTD.
-
- Amami Head Office
- 1260 Taira, Kasari-cho, Amami-shi, Kagoshima 894-0505 Japan (Map)
- Tel: 0997-63-0065
-
- Osaka Showroom
- 5-7-8 Hata, Ikeda-shi, Osaka 563-0021 Japan (Map)
- Tel: 072-754-0880
-
History
In 1905, Fujichika Higo, grandfather of Shuro, the founder of the company, started manufacturing Oshima Tsumugi in Kasari Town. He mastered the techniques of the fastening machine and started manufacturing. In the Taisho era (1912-1926), the Oshima Tsumugi Industrial Association was formed, and he worked hard as a member of the association.
In the 1960s, Fujichika's sons and others gathered together technicians skilled in various processes to establish an integrated factory that was capable of handling everything from the production of high-quality yarns to the manufacture of finished products. At the same time, the company promoted production efficiency, organized machine shops, and developed a network of wholesalers, department stores, and dealers throughout the country.
In 1968, then-Emperor Hirohito and Empress Nagako visited the factory, with another visit made by then-Crown Prince and Princess Akihito and Michiko in 1972. Prince and Princess Nobuhito and Kikuko, as well as Prince and Princess Masahito and Hanako, have also paid visits to the company.
In 1972, Shuro established the Authentic Amami-Oshima Tsumugi Cooperative, consisting of 10 manufacturers in Amami-Oshima and Kagoshima, and became its representative director.
In 1998, Oshima Tsumugi Museum Co., Ltd. was established, the trademark for “Oshima Tsumugi Art Museum” was acquired, and business expanded nationwide.
In 2005, Hotel Thida Moon opened on Amami-Oshima Island.
Today, he continues to produce unique products together with craftsmen of each process of authentic Oshima Tsumugi.
-